Hasami is a small town in Nagasaki Prefecture in southern Japan that has been producing porcelain and ceramics for over 400 years. From early on, division of labor was established; specialized mold-makers, clay-makers, and kamamoto (those who decorate and fire the ceramics) work together to manufacture affordable everyday tableware.
With kiln chimneys dotting the skyline and even the bridges decorated with ceramics, the visitor is constantly reminded of Hasami's rich heritage.
With kiln chimneys dotting the skyline and even the bridges decorated with ceramics, the visitor is constantly reminded of Hasami's rich heritage.
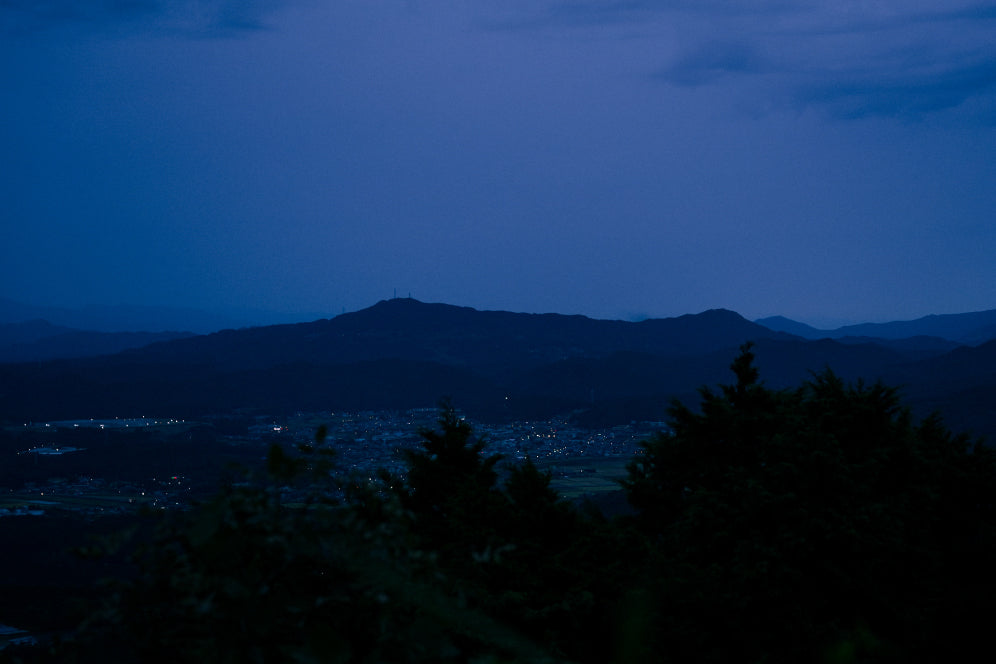
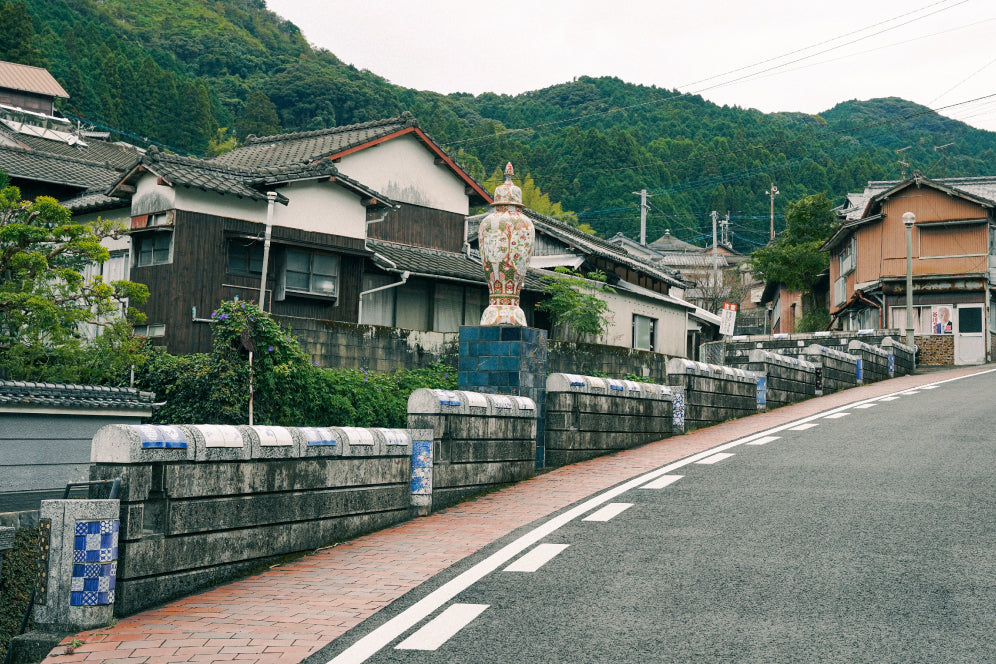
KINTO’s CLK-151 is one of the many collections produced in Hasami. By learning from traditional Hasami techniques of blending clays and controlling humidity and temperatures, we developed the shape, look, and feel of this product in collaboration with the local craftsmen. Each step is essential to bringing CLK to life.
Clay-making
The clay for CLK-151 is a blend of local “sandstone” pottery clay and a traditional porcelain clay from the Hizen district called Amakusa-toseki. A granular grade of Amakusa stone called zarame is mixed in to give the base its unique earthy texture.
The clay for CLK-151 is a blend of local “sandstone” pottery clay and a traditional porcelain clay from the Hizen district called Amakusa-toseki. A granular grade of Amakusa stone called zarame is mixed in to give the base its unique earthy texture.
Chamfering
To streamline production, machines are used for some of the molding process but the final touches like chamfering are done by hand. Stroke by stroke, the edges are removed to realize the CLK design. The subtle edges and rounded contours are the work of pure craftsmanship.
To streamline production, machines are used for some of the molding process but the final touches like chamfering are done by hand. Stroke by stroke, the edges are removed to realize the CLK design. The subtle edges and rounded contours are the work of pure craftsmanship.
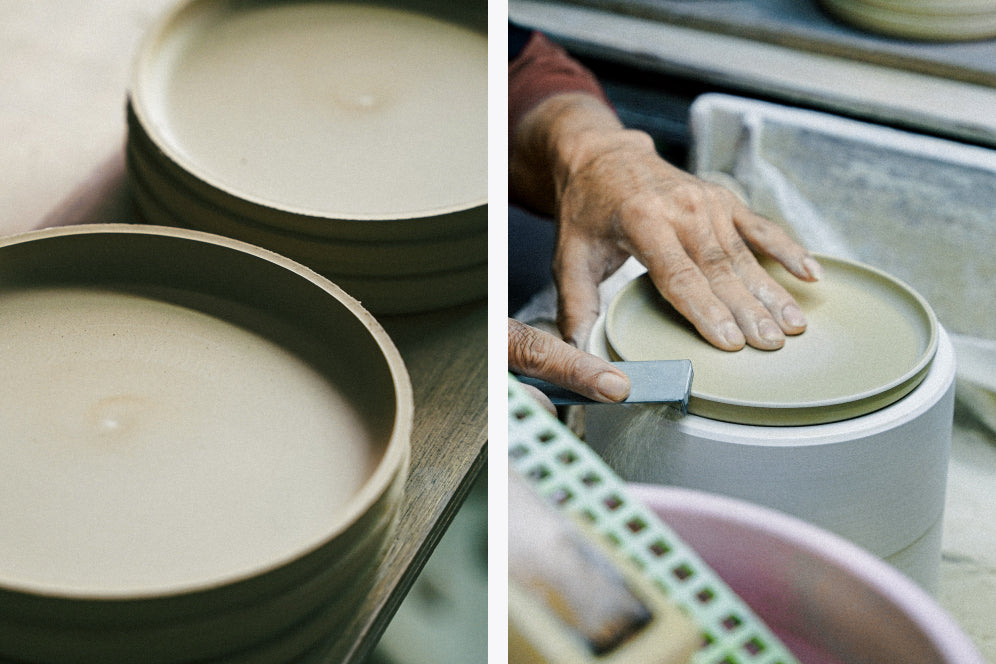
Glazing
After bisque firing and application of the logo, it is time for glazing. The base is coated with water repellent so it will reject the glaze. The pieces are then dipped into the glaze using special tongs. Even this deceptively simple process requires skill to achieve an even finish. The density of the glaze has been adjusted precisely to have the desired effect on the CLK clay.
After bisque firing and application of the logo, it is time for glazing. The base is coated with water repellent so it will reject the glaze. The pieces are then dipped into the glaze using special tongs. Even this deceptively simple process requires skill to achieve an even finish. The density of the glaze has been adjusted precisely to have the desired effect on the CLK clay.
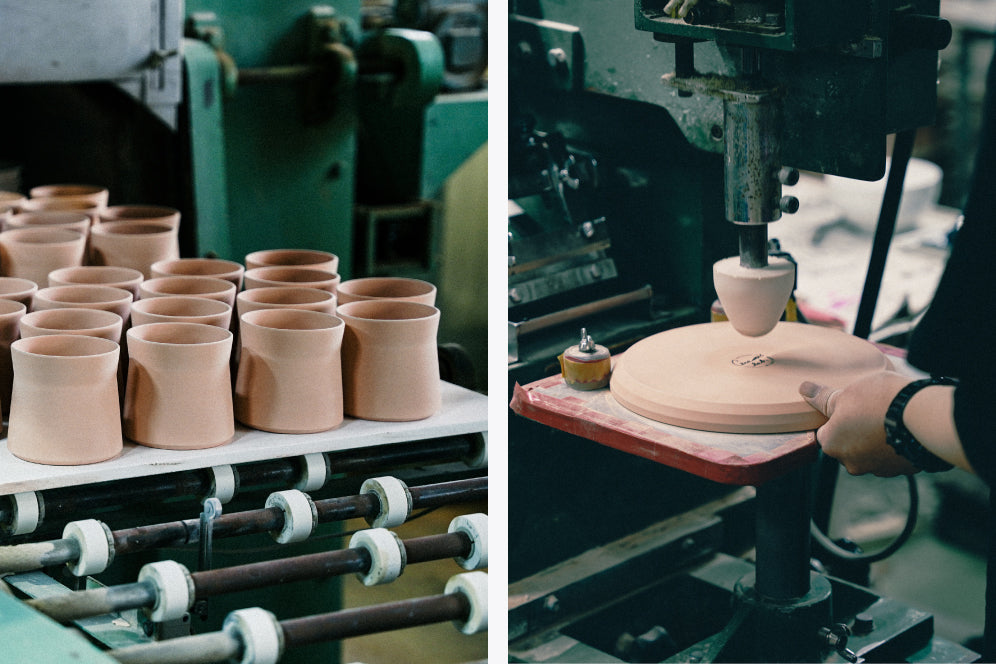
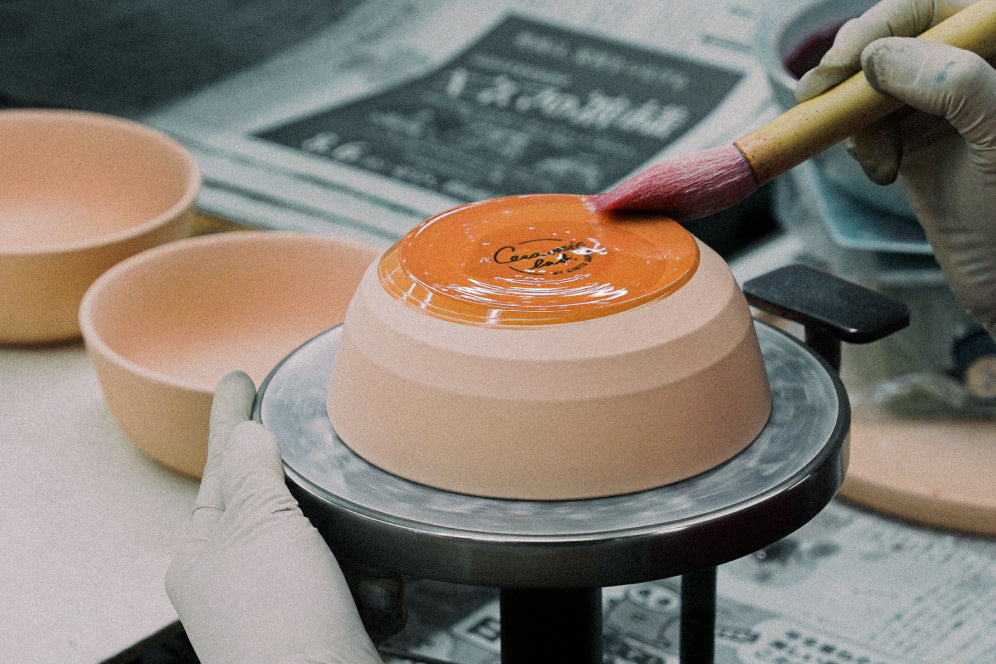
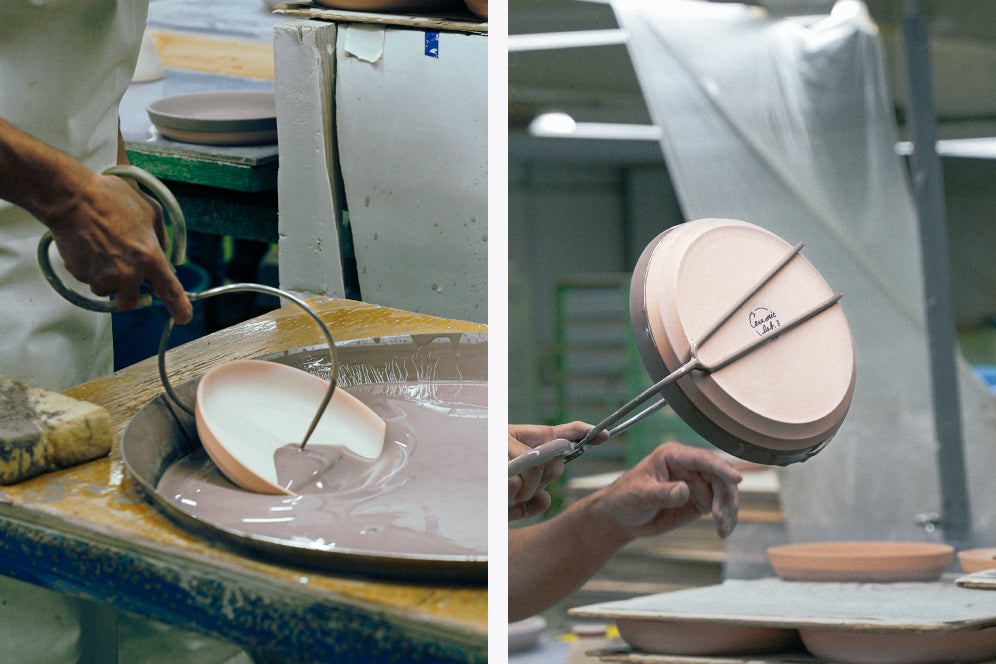
Final Firing & Inspection
Firing at a high temperature for a long time produces CLK-151’s signature matte texture and feel. Temperature and humidity conditions can impact the finish significantly, so the conditions in the kiln are expertly controlled according to the weather and the season. Mugs are placed on slanted props so the rim does not droop with the weight of the handle. After firing, each piece is carefully inspected to ensure consistent quality.
Firing at a high temperature for a long time produces CLK-151’s signature matte texture and feel. Temperature and humidity conditions can impact the finish significantly, so the conditions in the kiln are expertly controlled according to the weather and the season. Mugs are placed on slanted props so the rim does not droop with the weight of the handle. After firing, each piece is carefully inspected to ensure consistent quality.
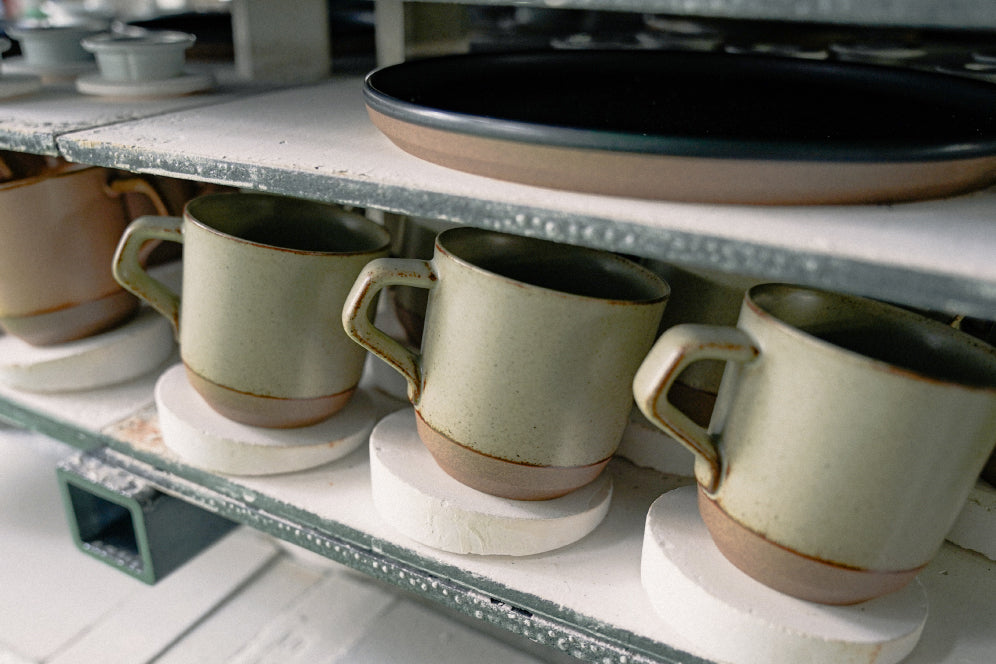
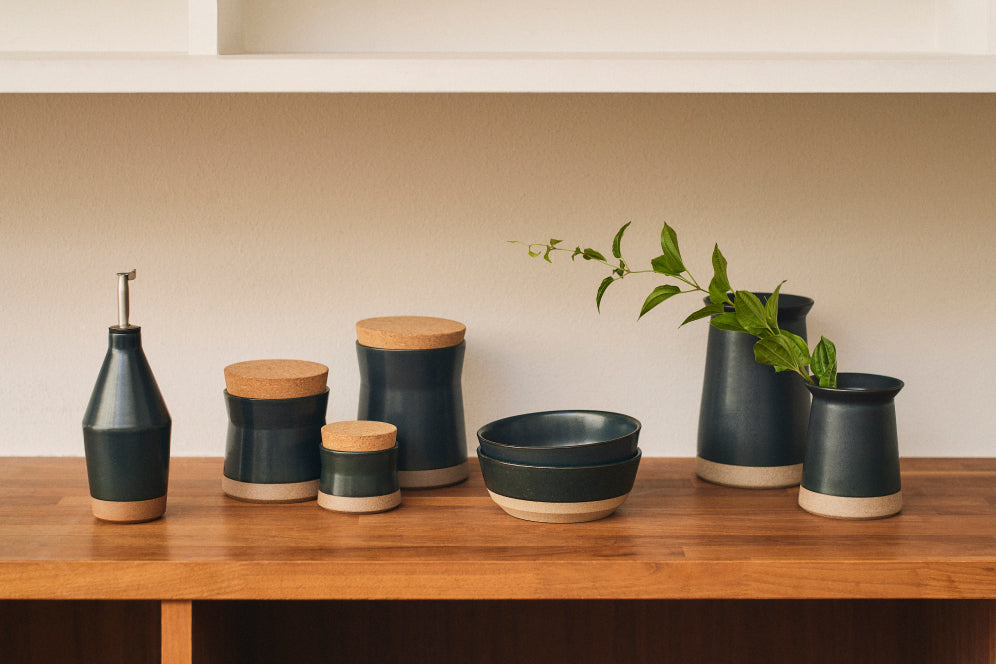
CERAMIC LAB is an interpretation of Japanese tableware to suit modern lifestyles, born from the partnership between KINTO and craftsmen who have carried on traditions. Its humble, earthy textures and calm colors add warmth to everyday life.